Hydraulic vs. Mechanical Disc Brakes? Heavy Equipment Needs Both
Share this
You’ll typically find two types of brakes on a piece of heavy equipment: hydraulic and mechanical. Why are both needed? Which brakes perform tasks that the other cannot?
One type of brake doesn’t satisfy all the performance and safety needs of heavy equipment – both are needed in combination – yet each performs different functions. A garden tractor, for example, uses hydraulic service brakes during normal driving operations to control the vehicle; parking brakes, which are mechanical, are used to keep the vehicle stationary when needed.
The chart below outlines the primary features, benefits, and characteristics of both, and how each meets the needs of heavy equipment vehicles.
Hydraulic vs. Mechanical Disc Brakes
Benefits and Performance Expectations
Brake Use in Heavy Equipment
Not only do hydraulic and mechanical brakes function differently, but their functionalities translate to distinct benefits of each.
Hydraulic Brakes
- Offer efficient braking performance with minimal effort from the operator
- Provide consistent braking power – critical when hauling heavy loads and/or operating on rough terrain
- Allow for precise control, enabling the operator to adjust braking power as needed
Mechanical Brakes
- Provide a redundant braking system in case the hydraulic system fails, ensuring that the vehicle can be brought safely to a stop if the primary system fails
- Are designed to provide a reliable and secure hold, especially on inclines or uneven surfaces
By combining hydraulic and mechanical brake systems, heavy equipment vehicles get the benefits of each system while mitigating their respective “weaknesses” – a highly effective pairing that helps ensure safety, reliability, and control.
Talk With a Hayes Brake Expert
Hayes designs and manufactures a variety of hydraulic and mechanical brake options for heavy equipment. Hydraulic options, such as the 1-663-1S are designed for easy mounting. Mechanical brake options, such as our M110LM, are lightweight and can handle clamp forces of 10,000 pounds.
We encourage you to reach out today – we’re eager to help identify the ideal brake solution for your heavy equipment.
Subscribe to our blog!
Related blogs
Section Intro
Help visitors get the basic idea within a few seconds, so they understand what this section is about.
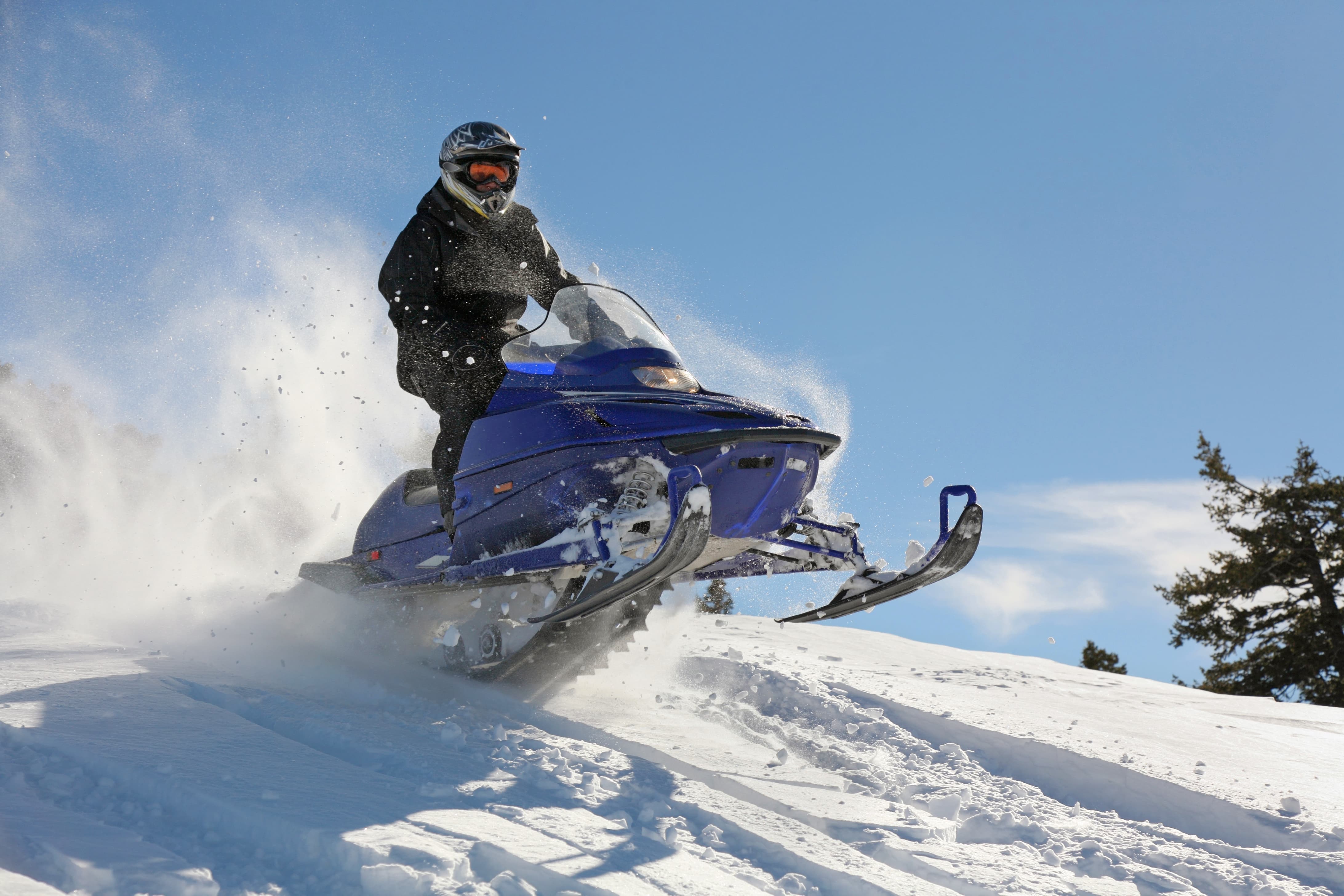
How Powersports Brakes Manufacturers Can Meet Extreme Demands in Performance
For snowmobile riders, UTV enthusiasts, and anyone else hitting the trails, the U.S. has its share of extremes in weather and terrain — and they’re some of the biggest challenges powersports vehicles...
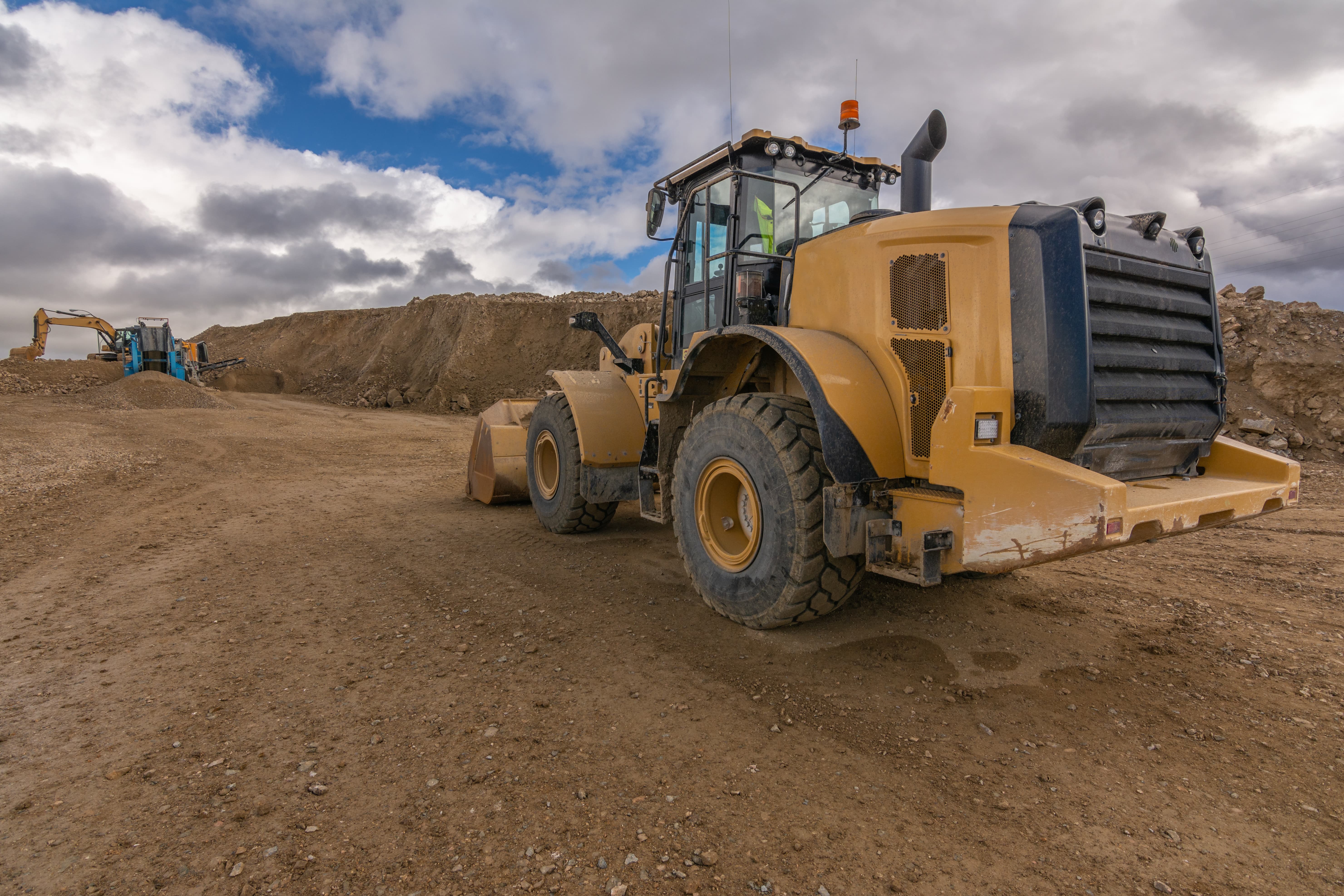
Spring Applied Hydraulic Release Brake Actuator: 4 Benefits for the Construction Industry
In 1990, Hayes Performance Systems patented its Spring Applied Hydraulic Release, or SAHR, brake actuator (initially called the Spring Applied/Pressure Release Emergency Brake Actuator) as a...

Dry Disc Brakes: How Engineering Impacts Performance & Safety
Dry disc braking systems, when they came into widespread use decades ago, represented a significant improvement over drum brakes. They’ve been used ever since in everything from mountain bikes to...